The ET-SP2 positioner is used for pneumatic linear or part-turn actuators. The positioner moves the actuator to a valve position corresponding to the setpoint from 4-20mA signal or computer binary singal.
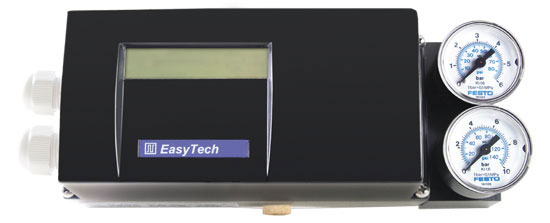
Using piezo technology, the position can replace directly the traditional positioner with spray nozzle. Position feedback module, limit switch module, HART module and other bus modules can be supplied as option.
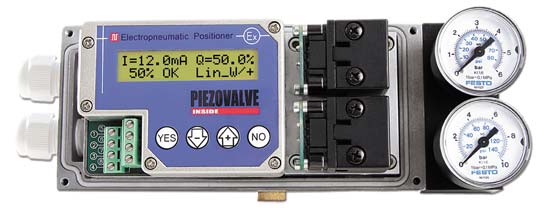
Using Fuzzy PID control software, the positioner can auto select fine valve-parameters by itself , running fast, steadily and accurately. With a 32-character LCD and four input keys, the valve can be operated easily at the scene, do not need other equipment.
The positioner can detect and sign any abnormal change on the actuator and valve. This information is important for diagnosis of the actuator or valve.
The positioner can detect and sign any abnormal change on the actuator and valve. This information is important for diagnosis of the actuator or valve.
Functions
-
Simple operation
Local operation and configuration of the device using four input keys and 32-character LCD Auto Calibrate
The positioner can be auto calibrated and configure the parameters such as normal-open or normal-close actuator, zero point and full-scale point. The process will spend few minutes.-
Ultra Low air consumption and short responding time
The positioner uses the Piezo Valve (product by HOERBIGER-ORIGA in Germany)unit as electropneumatic driver,with operating voltage at 24 VDC@10μA, responding time less than 20mS. The valve was precisely regulated in a short time. Low air consumption will save utility cost.
Application
The ET-PS2 positioner is available:
• For single-action actuators
• For linear actuators
• For part-turn actuators
• For hazardous applications: ExiaIICT6 certificated (intrinsically-safe device)
Mechanical Protection & EMC
Protection: IP65
Resistance to Vibration: 8g
Casing & Internal Meterial: molded aluminium & surface oxidized
Coating: antifouling paint
Using 3 layers of metals casing,the positioner can resist or absorb any noise from outside and signal cable.
![]() |
Display the basic parametes |
Manual set | |
Auto calibrate(see the process in figure.2) | |
Select flow curve or defineite a flow curve | |
Select Way/Angle/+/- | |
Set the response value of limit switch | |
Set out mode of limit switch | |
Set the sensibility: six options. | |
Set range split: OFF/4-12mA/12-20mA | |
... | |
Select the chamber size | |
Figure.1 The parametes |
![]() |
Detect zero position |
Detect the direction of action | |
Detect full-scale value | |
Detect exhausting time | |
Detect full-scale time | |
move to points: 0% | |
move to points: 25%,50% and 75%, | |
move to points: 100% | |
move to the point:75%,50%,25%and 0% | |
Display hysteresis at the point 25% | |
Display hysteresis at the point 50% | |
Display hysteresis at the point 75% | |
Finish and save the result | |
Figure.2 Auto Calibrate Process |
Order Instructions
Types | ET-SP2-A | ET-SP2-A-P | ET-SP2-A-L | ET-SP2-A-L |
Descriptions | Basic device | Basic device with Position Feedback |
Basic device with limit switch |
Basic device Position Feedback & limit switch |
System Input |
2-wire 8.4v 4.0-20.0mA |
2-wire 8.4v 4.0-20.0mA |
2-wire 8.4v 4.0-20.0mA |
2-wire 8.4v 4.0-20.0mA |
Ui=28VDC Ii=93mA Pi=0.65W Ci=0μF Li=52μH |
Ui=28VDC Ii=93mA Pi=0.65W Ci=0μF Li=52μH |
Ui=28VDC Ii=93mA Pi=0.65W Ci=0μF Li=52μH |
Ui=28VDC Ii=93mA Pi=0.65W Ci=0μF Li=52μH |
|
Position Feedback Output |
9-36VDC 4.0-20.0mA |
9-36VDC 4.0-20.0mA |
||
Ui=28VDC Ii=93mA Pi=64mW Ci=0.04μF Li=0mH |
Ui=28VDC Ii=93mA Pi=64mW Ci=0.04μF Li=0mH |
|||
Limit Switch Output |
8-26V/2-wire NO/NC OFF:<0.6mA ON:>4.0mA DIN19234 |
8-26V/2-wire NO/NC OFF:<0.6mA ON:>4.0mA DIN19234 |
||
Ui=15.5V Ii=20mA Pi=0.65W Ci=0.04μF Li=0mH |
Ui=15.5V Ii=20mA Pi=0.65W Ci=0.04μF Li=0mH |
|||
Intrinsically Safe marking |
ExiaIICT6 | ExiaIICT6 | According to the barrier and load |
According to the barrier and load |